As an integrated conveying device that integrates the functions of equal spacing and temporary storage, the drum conveyor is widely used in automated logistics systems. With the continuous advancement and innovation of modern logistics technology, the automation and flexibility of the logistics conveyor line are getting higher and higher. While the application of the roller conveyor is more common in the conveyor system, the user also puts higher requirements on the performance, cost, maintenance and service life of the equipment. This paper analyzes and explains the structure and control mode of two common stacking roller conveyors, and then explains the advantages and disadvantages of the two stacking roller conveyors.
1. Main structure The equipment is mainly composed of frame, legs, transmission device, swinging body, air control device, photoelectric detecting device and electronic control device. The mechanical brake is a swinging body and the whole structure
(1) Rack: The frame is assembled from special aluminum alloy profiles and strut assemblies, and is the main part of the load bearing materials and other components.
(2) Outriggers: The legs are assembled from special profiles and adjustable feet. The function is to support the frame and ensure the level of the conveying surface.
(3) Transmission device: The transmission device is composed of a reducer, a transmission belt, a pulley, a roller, etc. Its main function is to drive the transmission belt through the reducer, and the transmission belt friction roller rotates to realize the horizontal conveyance of the material thereon.
(4) Swing body: The oscillating body is composed of a connecting rod, a pulley, a swinging rod, a brake block, etc., and its function is to lift the belt when the pulley is lifted, and the brake block is disengaged from the roller, and the material is in a normal conveying state; When the wheel releases the belt and the brake block contacts the roller, when the roller is braked in the area, the material comes to the station and is immediately stopped.
(5) Air control device: The air control device is mainly composed of a solenoid valve, a cylinder and various pneumatic components. The external control signal or the detection signal of the dedicated photoelectric sensor is transmitted to the solenoid valve, and the solenoid valve is reversed to make the cylinder move, thereby driving the swinging body to obtain power or disengage power between the belt and the roller assembly to realize the material. Pneumatic schematic diagram of conveying and stopping, accumulating function
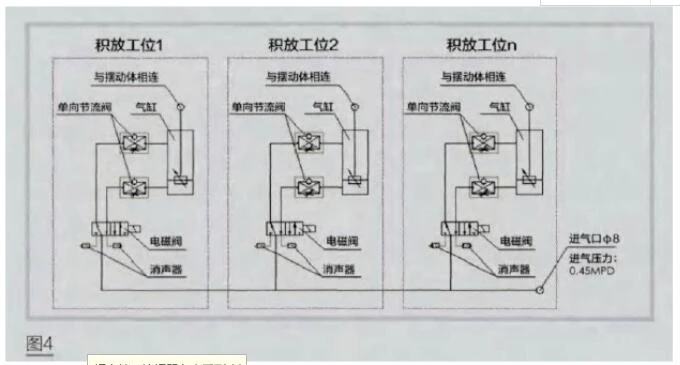
(6) Photoelectric detection device: The photoelectric detection device is divided into a line-controlled photoelectric detection device and a dedicated photoelectric detection device. The wire-controlled photoelectric detecting device is mainly composed of a photoelectric switch, a connecting plug and a photoelectric switch bracket. Its function is to detect the position of the material and feed back the signal to the electronic control system to achieve the control requirements required by the system. The dedicated photoelectric detecting device for accumulating is composed of a dedicated photoelectric sensor, a cable branching device and a connecting plug. A dedicated photoelectric sensor integrates a photoelectric sensor and corresponding logic components. The sensor is equipped with an input signal filter to eliminate interference from surrounding components or surrounding objects. When n dedicated photoelectric sensors are connected in series, the logic function integrated in each dedicated photoelectric sensor can ensure that the transported materials can be transported or stored in a single collision-free sequence.
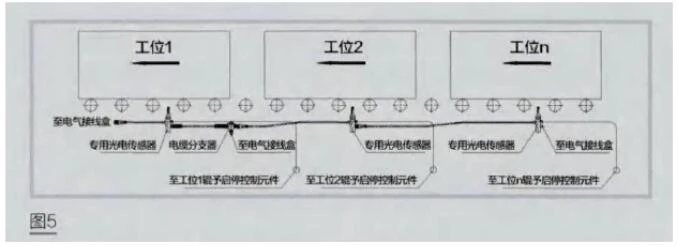
(7) Electronic control device: The electronic control device is composed of junction box, operation box and other electrical components, mainly to realize the electrical connection of the conveyor, so that it can operate normally.